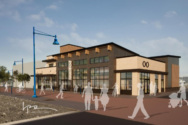
A Tri-City-area aviation enthusiast, raised by a father with a helicopter hobby, worked alongside his dad as a curious 12-year-old, often pedaling several miles on his bike to pick up parts for their projects.
Fast forward to the end of February this year. Nick Hertelendy of West Richland attended the 2018 Helicopter Association International Heli-Expo in Las Vegas to launch his creation – a prototype replacement blade and grip assembly for the Bell-47, which many recognize as the “M*A*S*H” helicopter.
“We (Hertelendy Research Associates) were contacted by the original equipment manufacturer to develop a new main rotor for the aircraft. They’re 20 feet long and sit on top of the machine. We’ve manufactured one set of prototypes,” he said. “If we get enough interest from the operators, we’ll move ahead with certification.”
About 1,500 of the iconic helicopters are still operational worldwide, a few locally – just outside the Tri-Cities, a couple near Dayton and in Pendleton, Hertelendy said.
In the late 1970s, Hertelendy and his late father bought a Scorpion 2 home-build helicopter kit.
“The blades on it were atrocious. So dad, being an enterprising guy, said, ‘I can do better than that.’ And we built a new blade. A friend of the family, an operator, had mentioned they had a hard time getting parts. He said, ‘Don’t waste your time; build something for us because we need it,’ ” Hertelendy said.
“We started with the intention of designing and building a set of blades for our own use on our own aircraft and ended up here,” he said. “It’s a hobby gone horribly wrong. We’ve been in production since 1996.”
Hertelendy quit his day job as a mechanical engineer about six years ago and has been creating and building aircraft parts for the past six years. His dad dedicated years to the company, starting daily at 6 a.m. He died in 2015.
The entire process for the Bell-47 replacement rotor blade — from planning stages to the complete build — took about four months. The most difficult part was building tooling to make extrusions. Extrusions are basically taking aluminum and having a die to shove it through, “like dough through a spaghetti maker,” Hertelendy said.
“I create a drawing that shows what I want the finished product to look like. Then I contract with a company to manufacture that component,” he said. The aluminum spars are 222 inches long and straight when they first come out, but when finished, are twisted. Pockets with trim tabs are produced and held into place by clamps.
“When it’s done, it looks like one cohesive piece but it’s actually lots of little pieces glued together,” Hertelendy said. The raw product is shipped to Scott’s-Bell and painted there.
Hertelendy said the process is slow, partly due to a “tremendous amount of checks and balances. The quality assurance program requirements for aircraft parts are comparable to NQA1 (used in the nuclear industry) – very rigorous,” Hertelendy said.
“These parts end up on commercial aircraft with passengers. They’re life-critical and non-redundant so you don’t want them to break,” he said.
Hertelendy is in negotiations with two other companies interested in doing projects and is working on a joint venture with an Australian company for a Bell-206 tail rotor.
“It used to be that we were producing products in competition with manufacturers,” Hertelendy said. “Now, we’re finding it easier to work with the manufacturers. I can design and build and let them market; they have the contacts. When the manufacturer needs one (rotor blade), they’ll just call to order it from me.”
It’s a streamlined process and one that makes it easier to focus on design and the building process, Hertelendy said.
“Now I have four clients instead of hundreds to manage. Instead of splitting the pie and struggling, we all work together and it’s much easier for everybody,” Hertelendy said.
The company’s largest current project is the replacement rotor blades for the Bell-47.
“These aircraft are primarily used for agricultural work and logging utility sling-loads. A few are for private owners, but it’s primarily a working machine,” Hertelendy said. Production of the helicopter ceased in 1974, with total production of about 1,600.
“I am very honored to be able to contribute in sustaining the Bell 47 helicopter fleet for the next few decades. I know that the dwindling availability of main roto blades has caused some concern for operators in the last few years,” Hertelendy said. “With this program, already initiated with the design and manufacture of a prototype blade and grip assembly, I am extremely confident to enter the STC (supplemental type certificate) certification phase and to have blade and grip assemblies ready for delivery in a timeframe of two to three years from now.”
The STC is designed to be fully compatible with the popular No-Bar-Kit, he said. Scott’s Helicopter Services is offering presale orders on Hertelendy’s creation, with a discounted price of $71,500 per set of blades and grips.
“Through this aggressive presale, it is paramount to understand that we need to receive enough orders to hit our minimum numbers in order to justify certification and production cost,” said Scott Churchill, Scott’s-Bell owner and president. He urged all Bell 47 operators “to seriously consider placing an order for this presale because if the program doesn’t advance, replacement main rotor blades will simply no longer be available, which risks the future of this beautiful helicopter.”
Hertelendy agreed.
“The difficulty is they (Bell-47 rotor blades) haven’t been manufactured since the 1980s and are getting in short supply. Unfortunately, the technology to produce the original blades is cost-prohibitive,” Hertelendy said. Instead the new blades are built of carbon fiber and aluminum, which makes them “more efficient,” he said.
The new composite main rotor blade and grip assembly, which is designed as a drop-in replacement for both the existing -21 and -23 blades and grips, will be offered as an SB47 owned STC for helicopters operating under the 2H1 and 2H3 Type Certificates, Churchill said.
“Current projections show an increase in performance of about 10 percent over the existing blades by simply utilizing a proven NASA airfoil design,” Churchill said. The assembly is designed to have a 5,000-hour life limit with no overhaul scheduled during its life, providing a true direct operating cost of $14.30 an hour, he added.
While attending the launch at the HAI event in Las Vegas, one of the largest civilian rotorcraft trade shows offered, Bell-47 operators were enthusiastic about the product, Hertelendy said.
“We’ll see if the enthusiasm translates to deposits put in escrow,” Hertelendy said. Regardless, HRA’s innovation will continue at its West Richland headquarters.